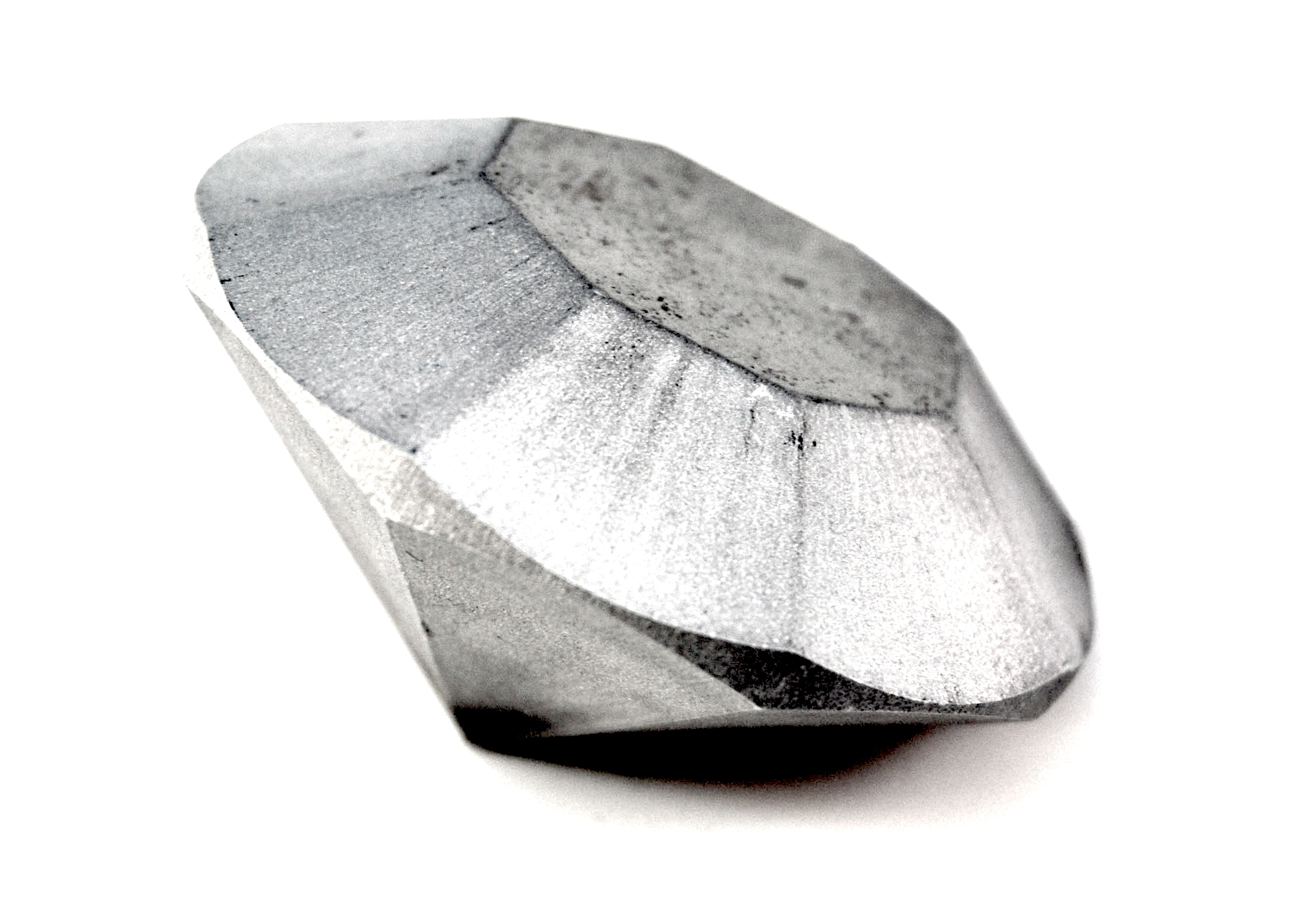
Comparative Cutting
Waterjets can cut any solid material including stone, tile, glass, metal, foam, rubber, plastic, and food.
When compared with plasma, laser, and EDM - waterjet cutting has distinct advantages. In addition to no heat-affected zone, the benefits and applications for waterjet technology are limitless and ever-expanding.
Process
![]() |
Waterjet | Erosion: using high-speed liquid sandpaper. |
![]() |
Plasma | Burning/Melting: using a high temperature ionized gas arc. |
![]() |
Laser | Melting: using a concentrated laser light beam. |
![]() |
EDM | Erosion: using an electrical discharge. |
Secondary Processing
![]() |
Waterjet | Usually none. Waterjet is a cold-cutting process that leaves a satin smooth edge. |
![]() |
Plasma | Typically, yes. Slag grinding for removal of HAZ (heat-affected zone) & flattening to eliminate distortion from heat. Assist gas used impacts depth of HAZ. |
![]() |
Laser | Sometimes yes. Removal of oxidized edge and HAZ. Gases used impact depth of HAZ. |
![]() |
EDM | Usually none. Very shallow HAZ imparted. |
Materials
![]() |
Waterjet | Virtually any material. |
![]() |
Plasma | Primarily steel, stainless steel, and aluminum. |
![]() |
Laser | A variety of materials, but primarily steel, stainless steel, and aluminum. |
![]() |
EDM | Conductive materials. |
Thickness
![]() |
Waterjet | Up to 24 inches, virtually any material. Z-axis constraint is only limit to thickness. |
![]() |
Plasma | Up to 2–3 inches, depending on the material. |
![]() |
Laser | Generally, 1 inch or less, depending on the material. |
![]() |
EDM | Generally, 12 inches or less. |
Part Accuracy
![]() |
Waterjet | Up to .001 inch |
![]() |
Plasma | Up to .010 inch |
![]() |
Laser | Up to .001 inch |
![]() |
EDM | Up to .001 inch |
Capital Investment
![]() |
Waterjet | $60k–$300k + |
![]() |
Plasma | $60k–$300k + |
![]() |
Laser | $200k–$1M + |
![]() |
EDM | $100k–$400k + |
Machine Setup
![]() |
Waterjet | Same setup for all materials. |
![]() |
Plasma | Different setup for different jobs. |
![]() |
Laser | Different gases and parameters for different jobs. |
![]() |
EDM | Different wire types for different jobs. |
Edge Comparison
With waterjet, you get a satin smooth edge right off the table. With other cutting
technologies there’s often secondary processing required to get that same satin smooth edge that waterjet produces.
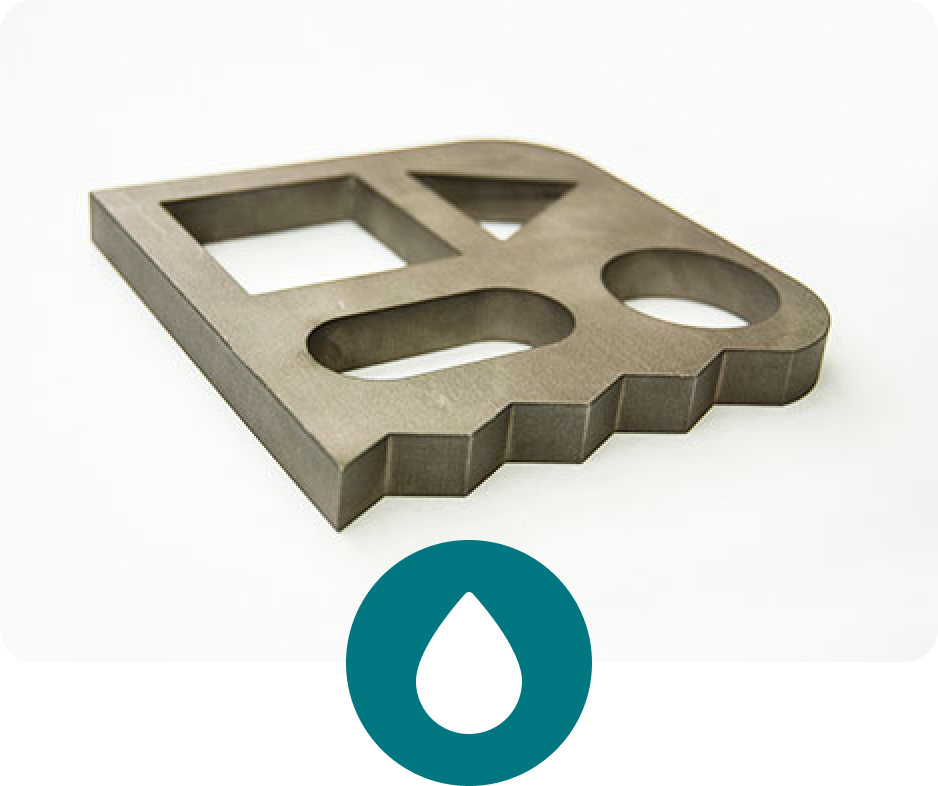
Waterjet
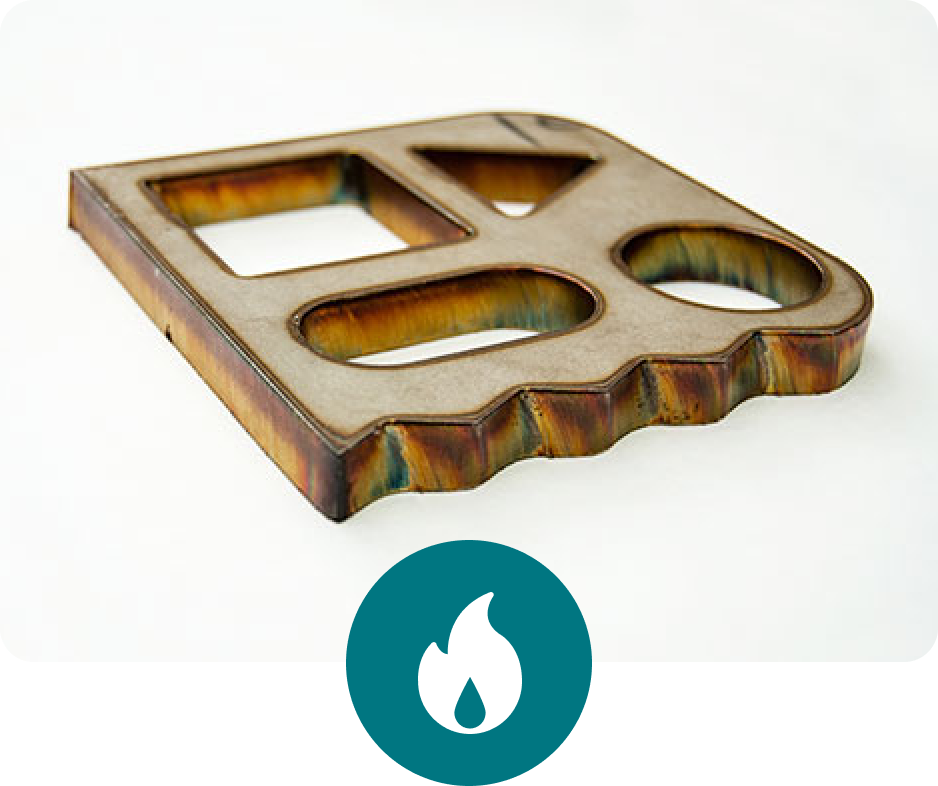
Plasma
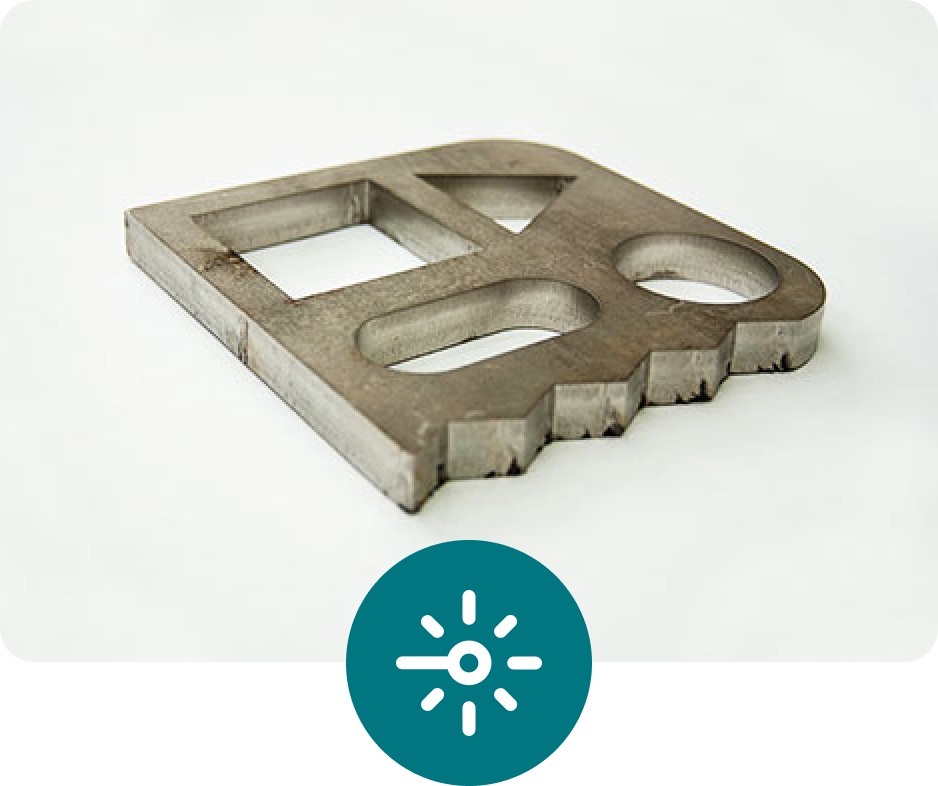
Laser
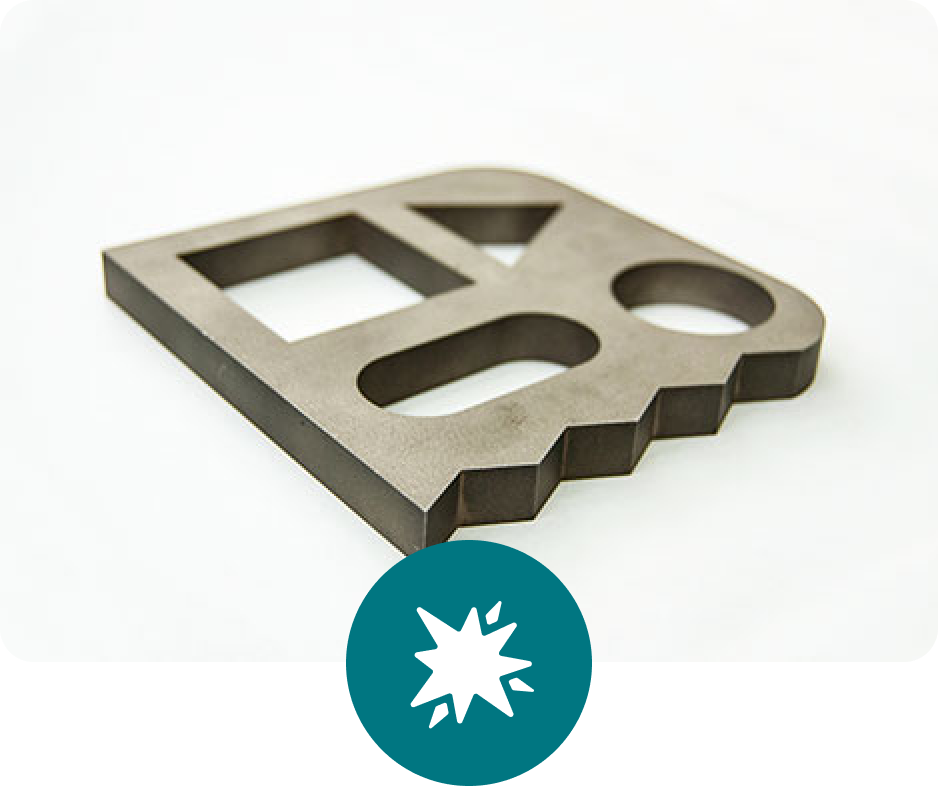
EDM
Cut Speed Range
There are clear benefits to each cutting method. Waterjet, in comparison with laser, plasma, and edm is an incredibly versatile process that allows you to cut thick or thin materials with ease. With waterjet, you get a satin smooth edge right off of the table – no secondary processing required.
There are clear benefits to each cutting method. Waterjet, in comparison with laser, plasma, and edm is an incredibly versatile process that allows you to cut thick or thin materials with ease. With waterjet, you get a satin smooth edge right off of the table – no secondary processing required.
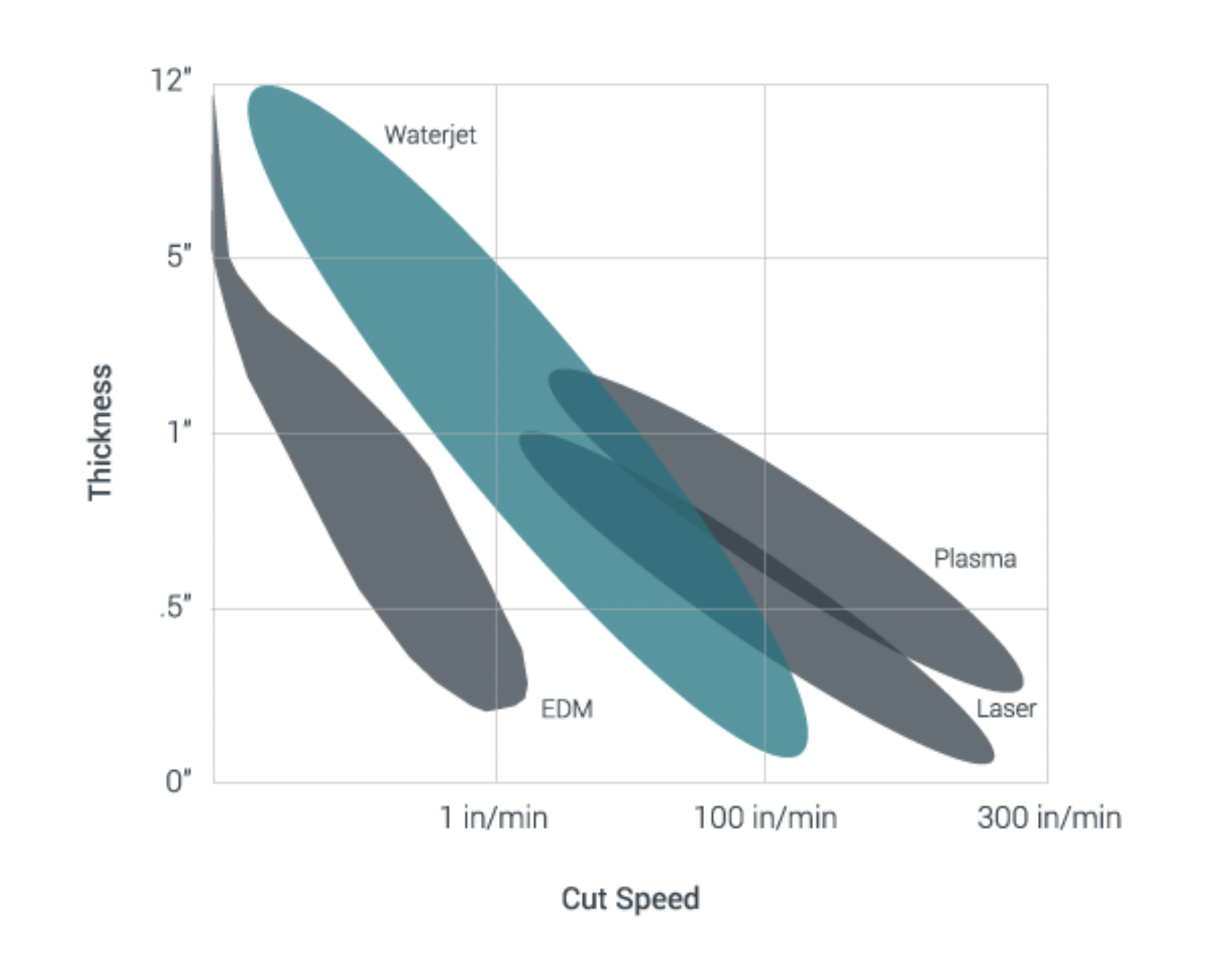