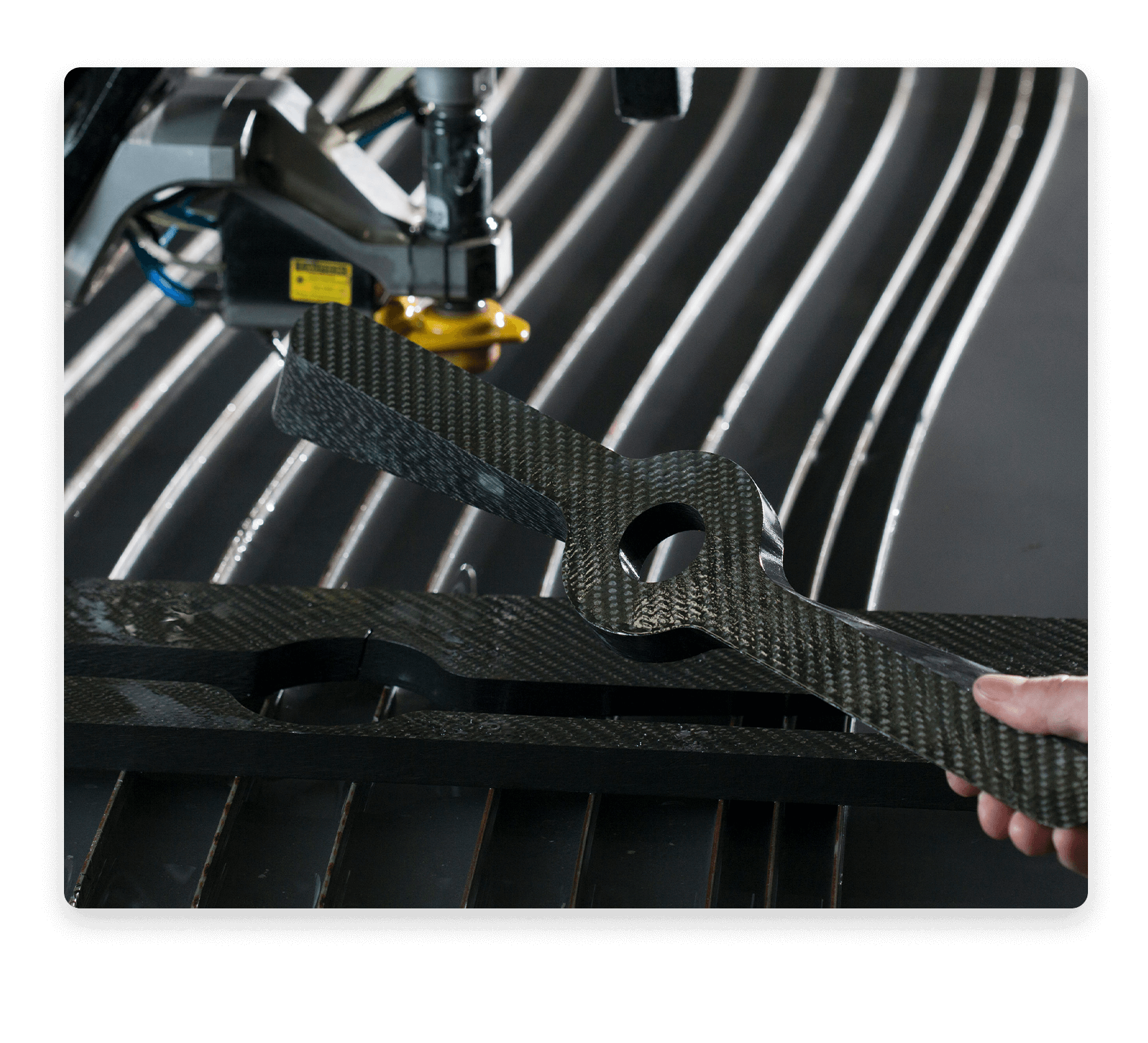
Cutting Composites with Waterjet
Today composites come in many forms including carbon fiber reinforced plastic (CFRP); fiberglass; and composite foams, plastics, paper, or metal. An abrasive waterjet's supersonic erosion can cut nearly any material, and the low contact force eliminates the need for bulky tooling. The finely focused jet of water cuts reliably and precisely in any direction to incredible detail. A Flow waterjet will rarely cause cracking, fraying, or delamination.Not sure a waterjet can handle your material?
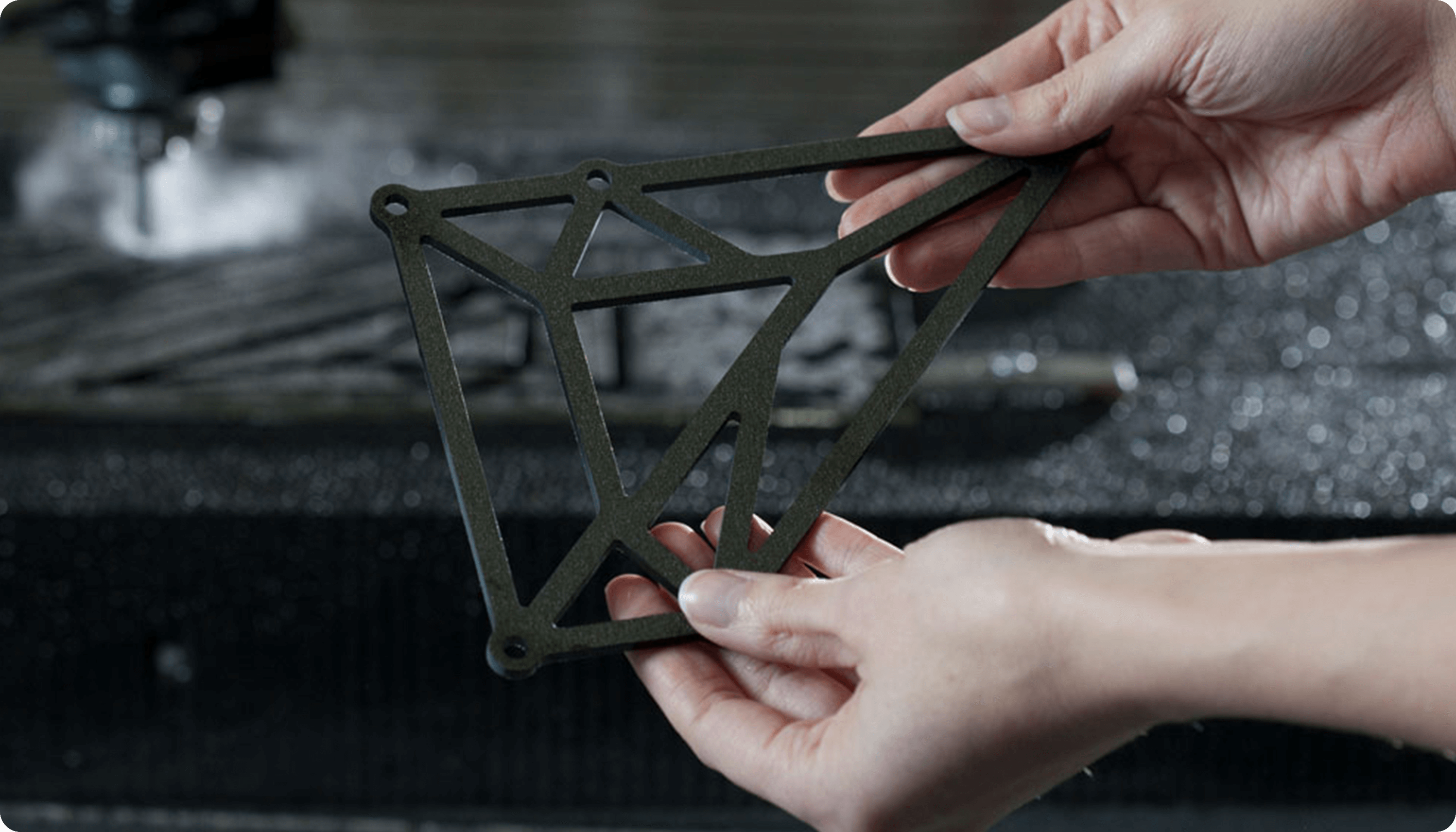
The Best Edge
Because abrasive waterjets cut by erosive action rather than friction and shearing, it leaves a satin smooth finished edge, free of frayed or delaminated areas. This minimizes the need for secondary finishing. Flow's waterjets can machine and pierce the material, eliminating expensive diamond tools, heat-affected zones, and complicated part supports.
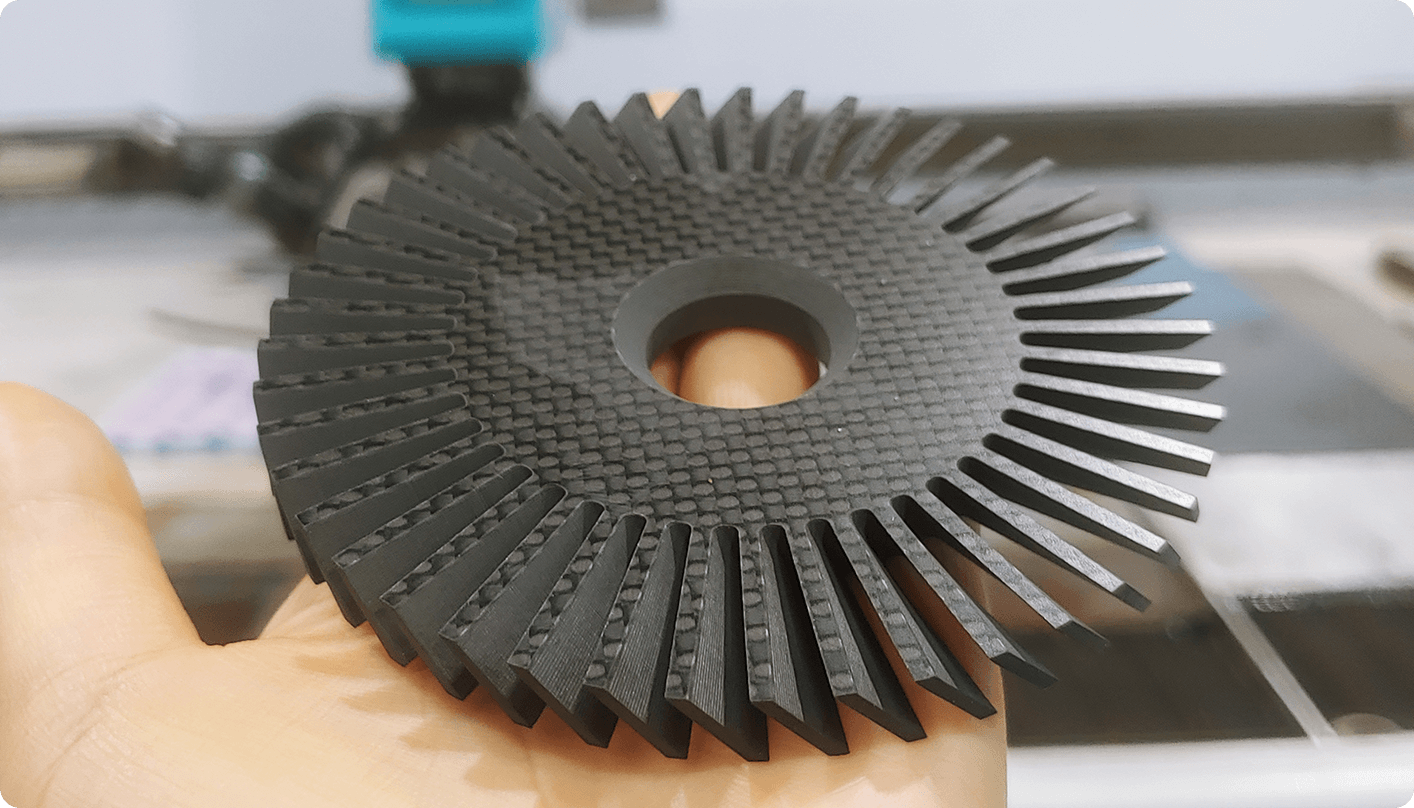
Minimal Kerfs
Cut composites 10 inches thick or 1/32 inch thick with the same tiny tool. Most Flow abrasive waterjets are 0.030 to 0.040" in diameter, and pure waterjets are approximately 0.005" in diameter.
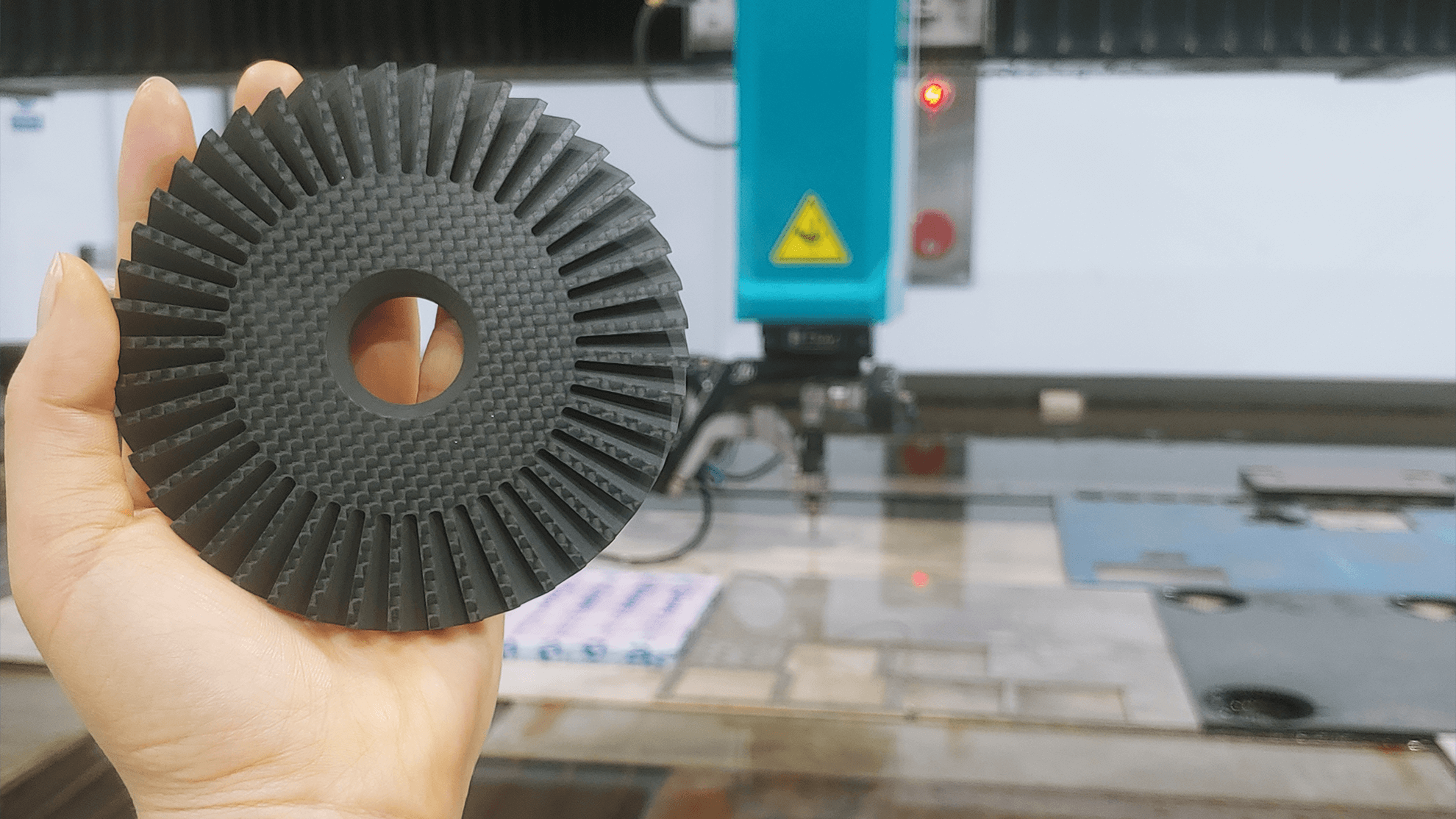
Key Benefits to Cutting Composites with Waterjet
- Increased productivity, fast cutting, and high-quality parts
- No delamination, whiskers, or fiber pull during cutting
- Minimal kerf allows incredible detail
- Raw material savings — reduced scrap
- Low operating cost — waterjet orifices and abrasive focusing nozzles require occasional replacement
- Omni-directional cutting, even at tight inside corners
- No need for extensive part clamping, minimal lateral or vertical forces
- Single-pass cutting, depending on material thickness
- No thermal damage
- Cut dust free
- Net or near-net cutting, little or no hand finishing
- Reduced tooling costs, lighter, flexible tooling