
Cutting Foam with Waterjet
Whether you're cutting foam for packaging, vehicle interiors, insulation, or other applications, the hair thin stream of a pure waterjet is an ideal way to cut the parts you need, fast. Waterjet reduces cut time, reduces consumables compared to traditional methods, and allows for the ultimate flexibility in material adjustments.Not sure a waterjet can handle your material?
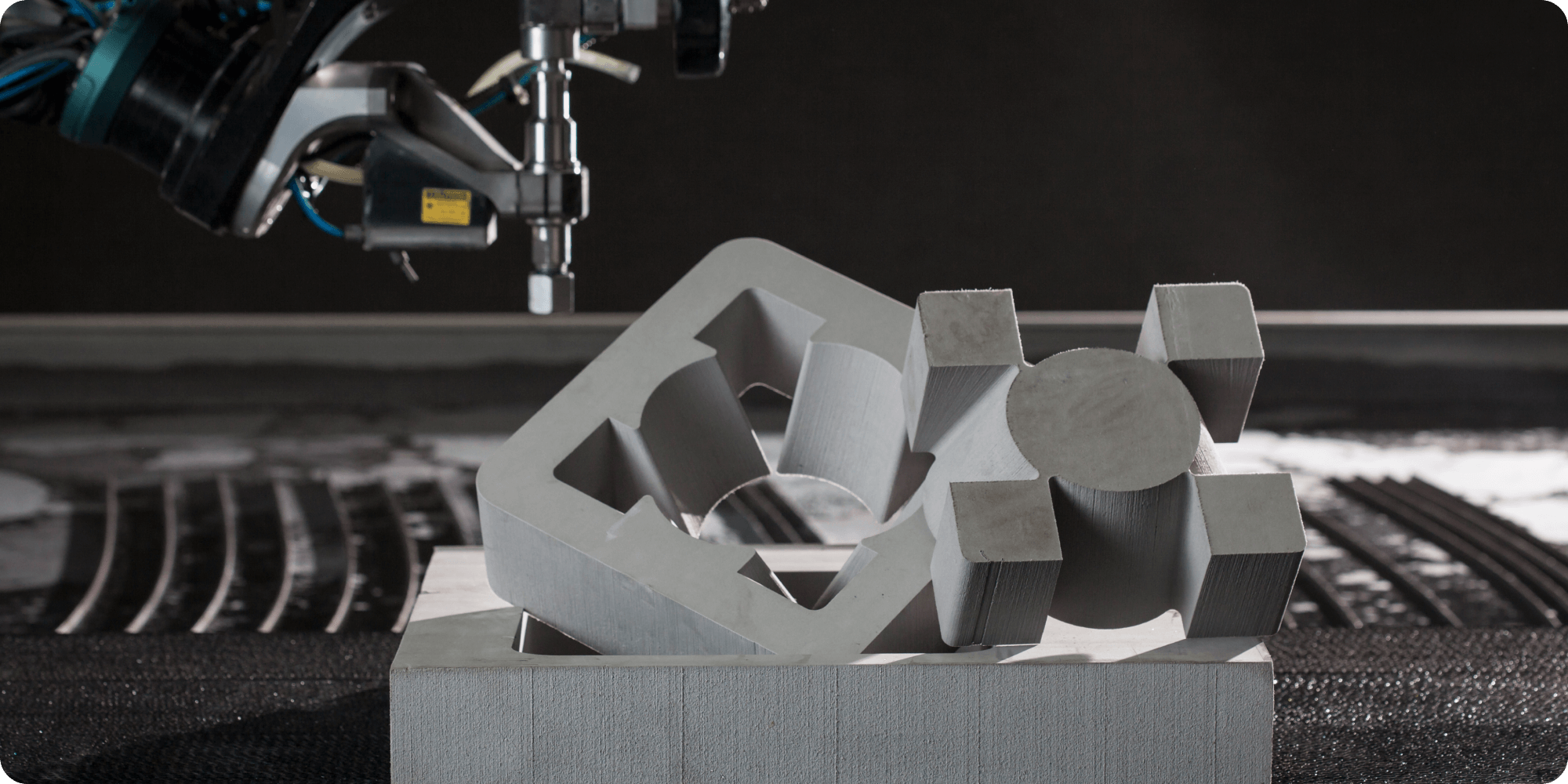
The Best Edge
Waterjet is a cold cutting process, meaning it doesn't generate heat during cutting. This eliminates the risk of melting or warping the foam, which can occur with other cutting methods. As foam is sensitive to temperature changes, waterjet cutting preserves the foam's structural integrity and produces clean, smooth edges.
The absence of friction and mechanical stresses minimizes any chances of deformation, tearing, or roughening of the foam's edge.
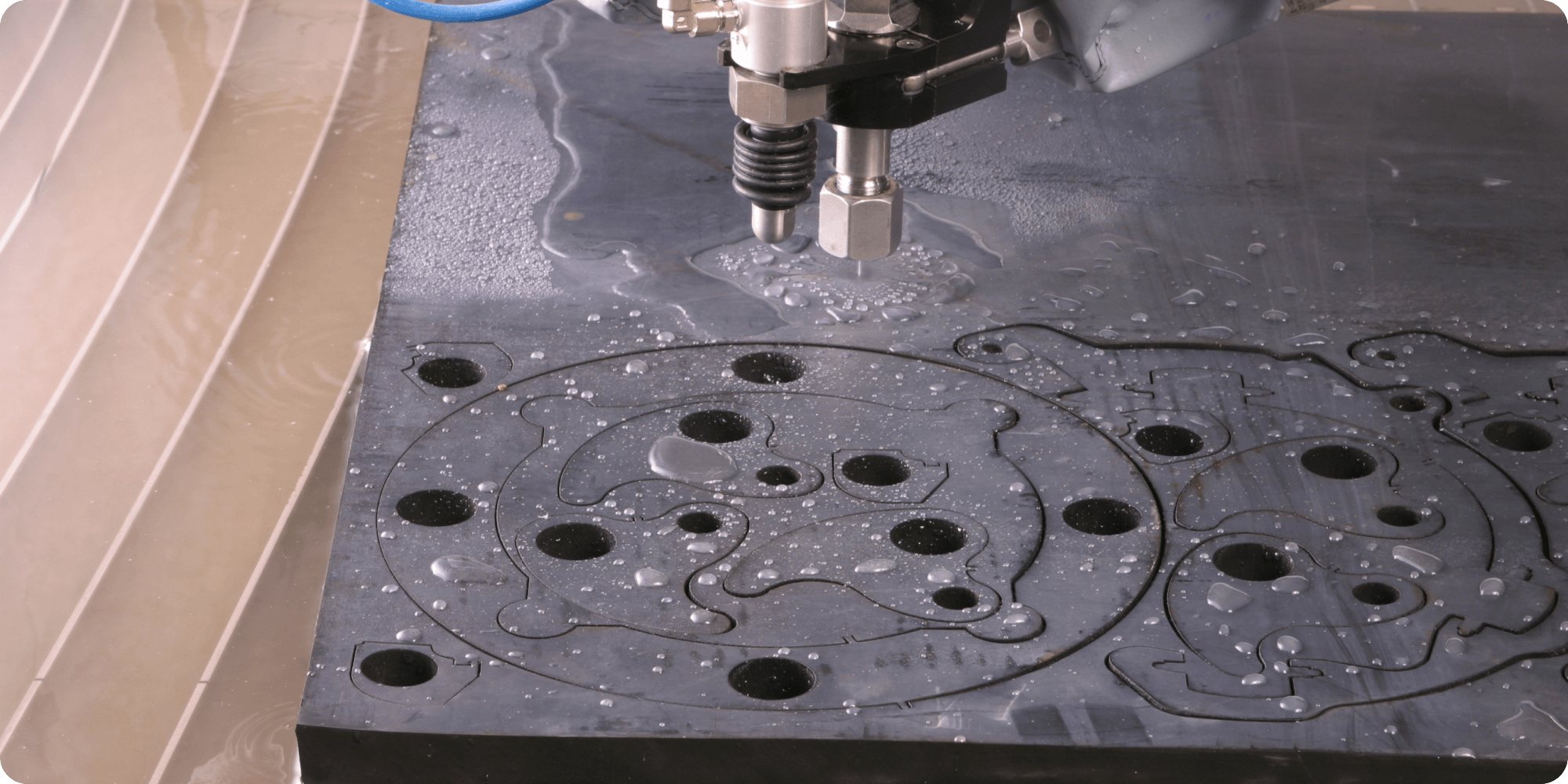
Minimal Kerfs
Compared to saws and knives, a waterjet's thin cutting width allows for nearly any design to be cut to perfection. A waterjet stream is sharp and precise, maximizing material utilization.
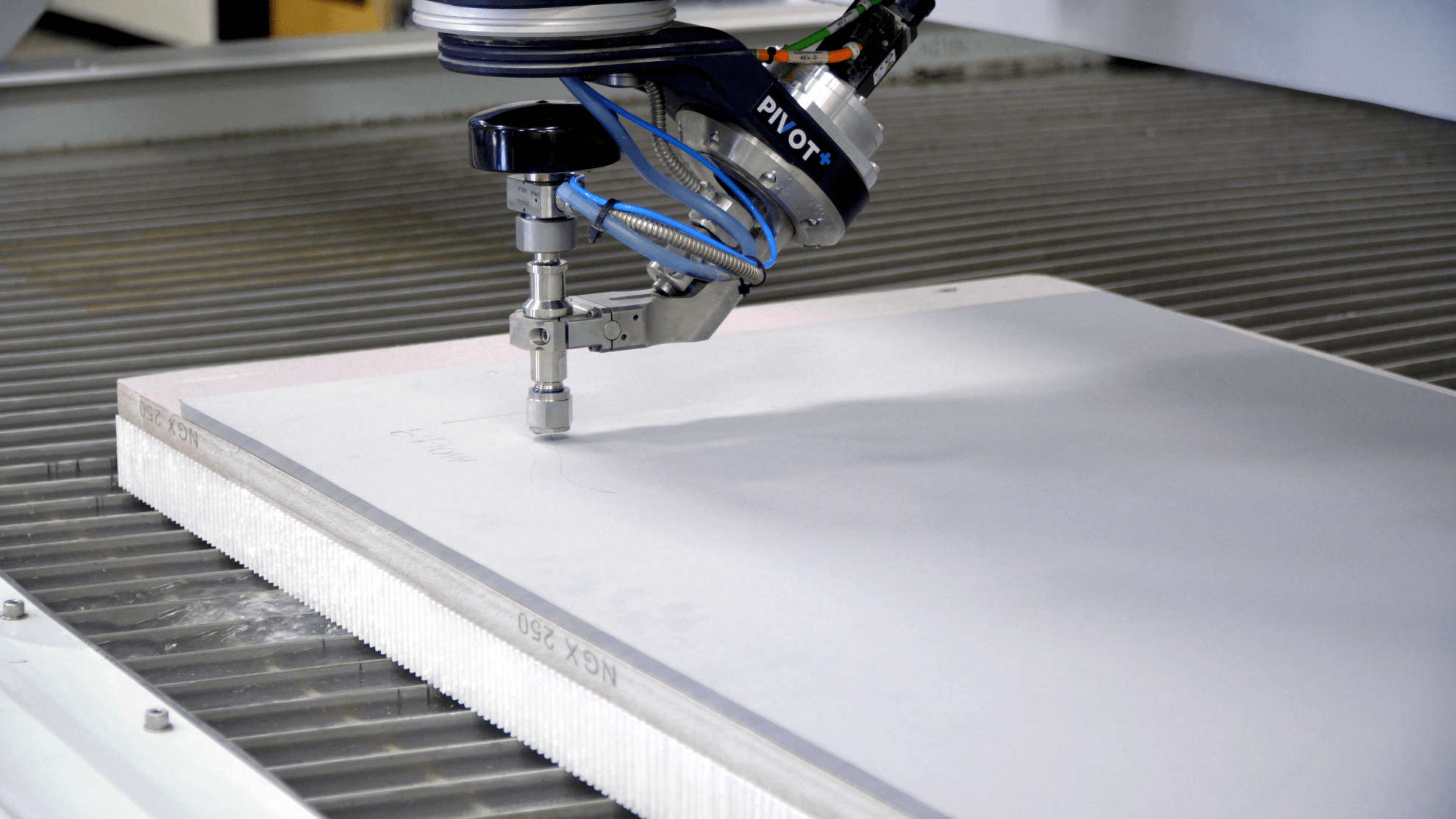
Key Benefits to Cutting Foam with Waterjet
- Increased productivity, fast cutting and high-quality parts
- Minimal kerf for the most detailed and artistic patterns
- Raw material savings — reduced scrap
- Low operating cost — waterjet orifices and abrasive focusing nozzles require occasional replacement
- Omni-directional cutting, even at tight inside corners
- No need for extensive part clamping; minimal lateral or vertical forces
- Single-pass cutting, depending on material thickness
- Net or near-net cutting, little or no hand finishing